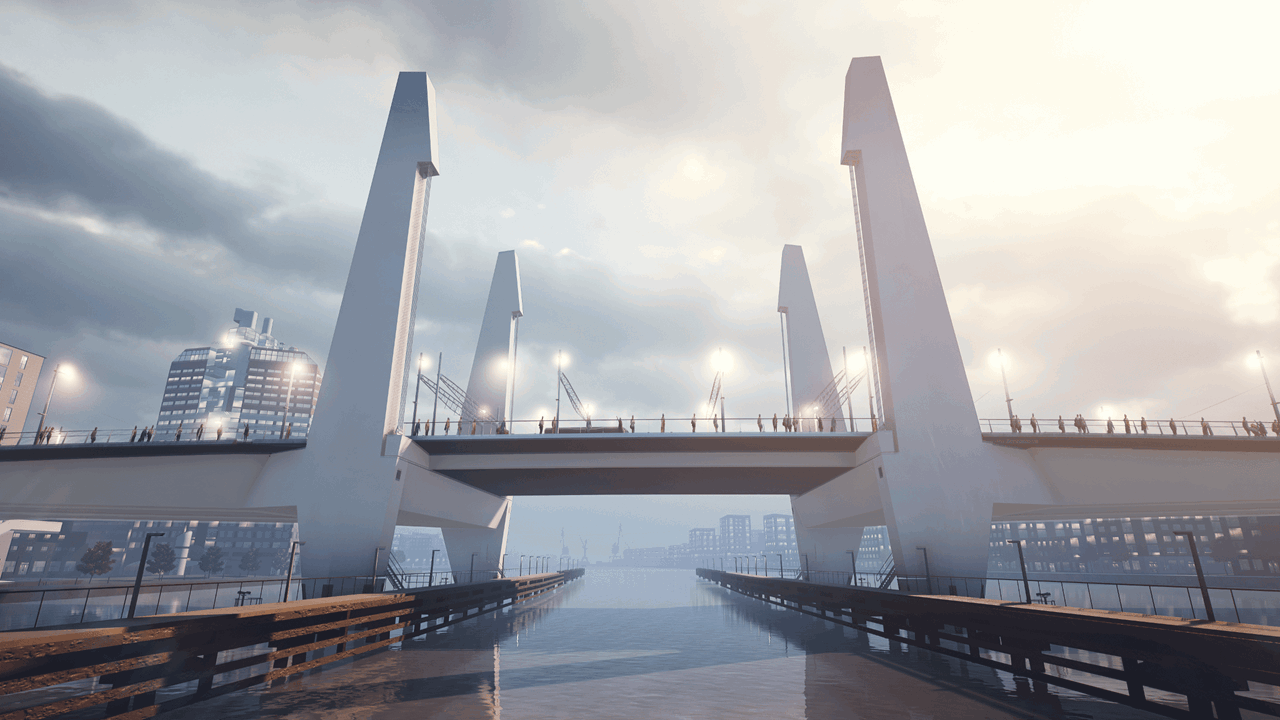
Ein neues wahrzeichen in Göteborg
In Göteborg entsteht mit der neuen Hisings-Brücke eine vertikale Hubbrücke, die Nord- und Südufer des Flusses Göta Älv miteinander verbindet und Schiffe passieren lässt. Die außerordentliche Aufmerksamkeit für Designdetails und Funktionalität hat dazu beigetragen, etwas zu schaffen, das größer ist als die Summe seiner Teile.
Im Mai 2021 wurde die Hisings-Brücke im schwedischen Göteborg für den Verkehr über den Fluss Göta Älv freigegeben. Zunächst für Autos, Busse, Fahrräder und Fußgänger – die Fertigstellung der Straßenbahnschienen wird im Laufe des Sommers erfolgen.
Die Planung des Projekts im Auftrag der Göteborger Verkehrsbehörde begann bereits 2009. Der Baubeginn war im Jahr 2016. Zuverlässigkeit und der Einsatz bewährter Technologien waren wesentliche Anforderungen in der Spezifikation für die Hubspannweite und ihre Maschinentechnik. Ein Konsortium aus Skanska und MT Højgaard gewann die Ausschreibung und leitet nun das Projekt.
Im Entwurfswettbewerb 2013 gab es Vorschläge für verschiedene bewegliche Brückentypen: Klappbrücken, Drehbrücken und Vertikalhubbrücken. Der Gewinner war die Vertikalliftbrücke Arpeggio, die von einem Konsortium aus Architekturbüros und Projektplanern entworfen wurde. Die Entscheidung der Jury konzentrierte sich auf Machbarkeit, Entwicklung und Funktionalität.
Die Brücke wird ein Symbol Göteborgs, ein Wahrzeichen der Stadt, im Einklang mit ihrem Charakter und ihrer Landschaft.
Viele Vorschläge, bevor der richtige gefunden wurde
Die Hisings-Brücke ist eine 440 Meter lange vertikale Hubbrücke. Wenn ein Schiff passieren muss, wird die zentrale und 28 Meter lange Hubspannweite angehoben. Diese wird von vier Stahltürmen (Pylonen) getragen. Nach jedem Anheben muss die Hubspannweite exakt auf die 12-Meter-Nivellierung zurückfahren, damit die Fahrstreckenbahnen des Hubteils perfekt an der Straße ausgerichtet sind.
Die Bauingenieure ELU konstruierten die Stahlpylonen und die Straße. Sie beauftragten Tikab Strukturmekanik AB mit der Entwicklung der Hubvorrichtung. Peter Lassfolk, Maschinenbauingenieur und Netzwerkadministrator bei Tikab, entwarf die Vorrichtung gemeinsam mit seinem Team.
Lassfolk sagt, die Hisings-Brücke sei eine seiner anspruchsvollsten Aufgaben gewesen:
„Die größte Herausforderung bestand darin, Maschinen zu entwickeln, die auf den begrenzten Raum passen. Das war kompliziert, und wir haben viele verschiedene Lösungen unter die Lupe genommen, bevor wir uns für die jetzige entschieden haben.“
Komplexes System für die Hubspannweite
Es ist von entscheidender Bedeutung, dass das 37 Meter lange und 800 Tonnen schwere Hubteil schnell angehoben und abgesenkt werden kann. Es ist an 16 Seilen befestigt, vier in jeder Ecke. Die Seile führen nach oben zu den Seilrollen auf den Pylonen und dann nach unten bis zu einem Gegengewicht. Vier dünnere Seile werden mit den Maschinen verbunden, die das Gegengewicht ziehen.
Wenn das Hubteil angehoben wird, wird das Gegengewicht nach unten gezogen. Wird das Hubfeld abgesenkt, wird die Hubkraft weggenommen, sodass das Gewicht des Hubfelds dafür sorgt, dass es unten bleibt. In jedem Pylon befinden sich zwei große Haken, die durch eine Winde die Hubspannweite nach unten ziehen und die Hubkräfte aufheben. Das Expander System ist an den Haken befestigt.
Tikab war für das Design verantwortlich und die SH Group hat die Maschinen hergestellt und getestet. Tikab schlug den Einsatz des Expander Systems vor und die SH Group stimmte diesem Vorschlag als beste Lösung zu. Das Expander System ist eine Lösung gegen Verschleiß von Gelenklagerungen und besteht aus drei Hauptteilen: Einem Bolzen in der Mitte und zwei Spreizhülsen, die direkt in die vorhandene Halterung eingebaut werden. Beim seitlichen Anziehen der Befestigungselemente werden die Spreizhülsen auf die konischen Bolzenenden gepresst, dehnen sich aus und passen sich der Montagebohrung an.
Zuverlässigkeit und lange Lebensdauer
„Wir verwenden einen extra großen, maßgeschneiderten Expander-Bolzen“, erklärt Lassfolk.
„Der Hauptvorteil liegt darin, wie er die Montage erleichtert hat. Wir mussten große Komponenten auf engstem Raum installieren. Aber durch die Verwendung des Expander Systems war es ein reibungsloser Arbeitsablauf.“
Die Verwendung des Expander Systems erhöht auch die Lebensdauer und minimiert gleichzeitig den Wartungsaufwand. Normalerweise führt die Achsbewegung zu einer Abnutzung der Gelenklagerungen, wodurch die Bohrungen mit der Zeit oval werden und sich das Spiel vergrößert.
„Mit dem Expander System lässt sich dieses Spiel beseitigen“, sagt Brian Troest, Country Manager für Dänemark und Schweden der Nord-Lock Group. „Der Bolzen muss kleiner sein als die Bohrung, durch die er geführt wird. Die Spreizhülsen gleichen jedoch diese Differenz zwischen dem Bohrungsdurchmesser und dem Bolzendurchmesser aus.
Überdauert jede andere Lösung
Durch Anziehen der an den Seiten befindlichen Schrauben oder Muttern wird die Spreizhülse über den Bolzen geschoben. Durch den Innenkonus der Hülse und den Außenkonus des Bolzens weitet sich die Hülse radial auf. „Dann erhält man ein sicheres Resultat, das keine Probleme verursacht und jede andere Lösung überdauert“, sagt Troest.
Seit Jahren setzt Lassfolk das Expander System nun schon in verschiedenen Entwürfen ein. „Es war naheliegend, diese Lösung für das Hisings-Projekt zu wählen. Natürlich wollten wir hochwertige Produkte verwenden“, sagt er.