A magazine about bolting technologies
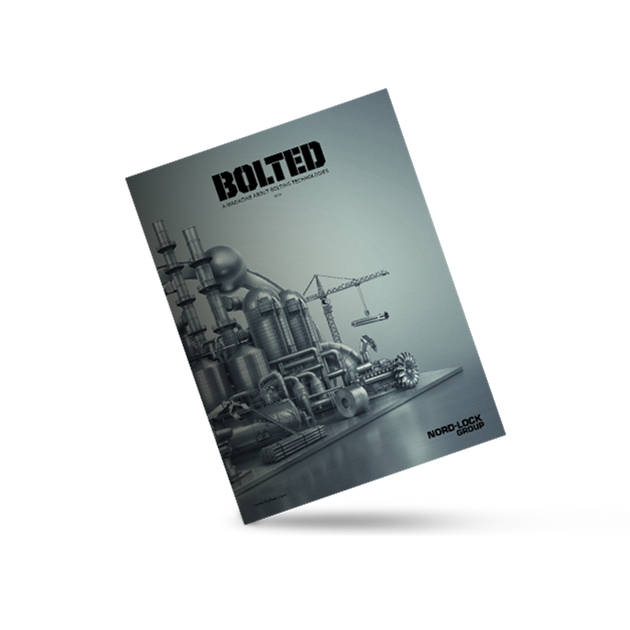
READ THE LATEST ISSUE
In one way, nothing’s new with this issue of Bolted. As always, you’ll find expert-curated content showcasing state-of-the-art bolting applications. But one thing’s for sure new: it marks the premiere of Bolted as a once-a-year publication, with some of the best digital content from the previous year.
In this issue, there is a strong focus on innovation: how our solutions bring efficiency and productivity gains to traditional industrial applications. From ensuring that decades-old hydropower facilities are ready to continue providing renewable energy for the coming decades, to maximizing the potential of wind farming, our four technology brands play a critical role in gearing up industries essential for our modern, and more sustainable, future way of life.
You’ll also get to learn about optimizing bolting in steel construction and explore how Expander makes it easier to conduct maintenance on machinery facing the toughest operating conditions out there.
All of the above and much more await you in this brand-new issue of Bolted.
Scroll down to read the articles!
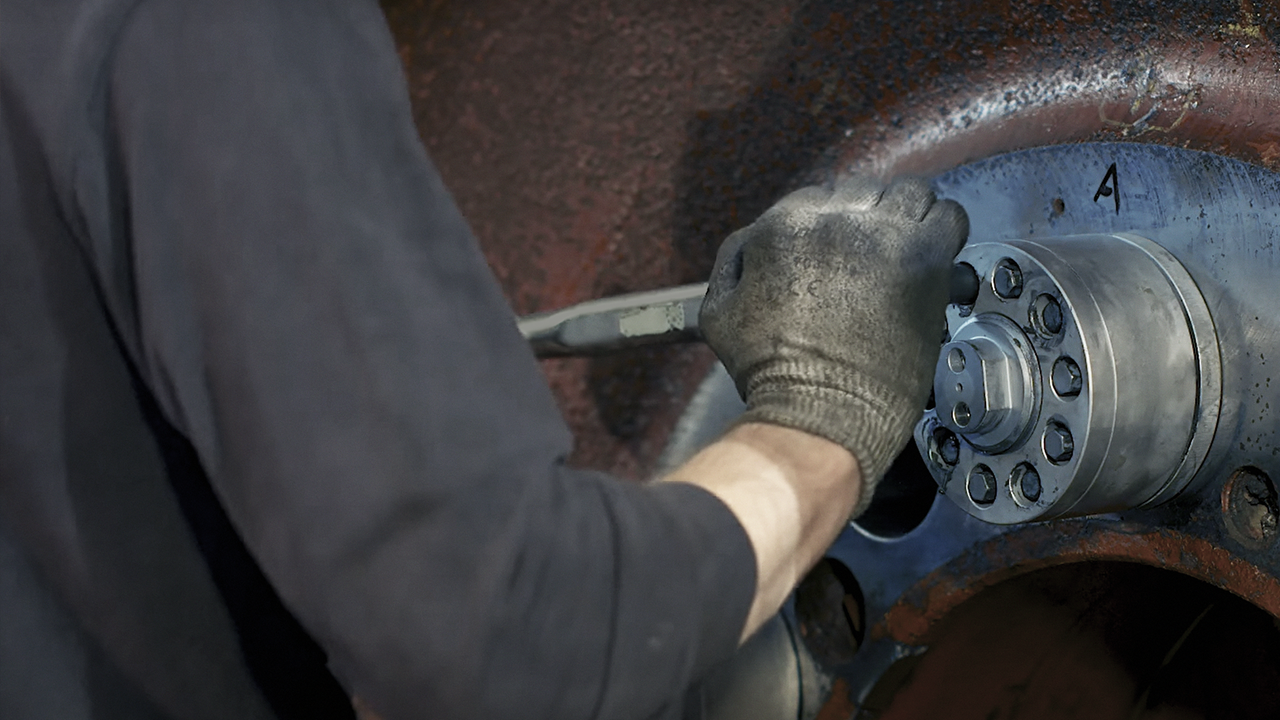
Explore how solutions from Nord-Lock Group support effective maintenance and secure operations in hydropower facilities
Read moreExplore how solutions from Nord-Lock Group support effective maintenance and secure operations in hydropower facilities
Read more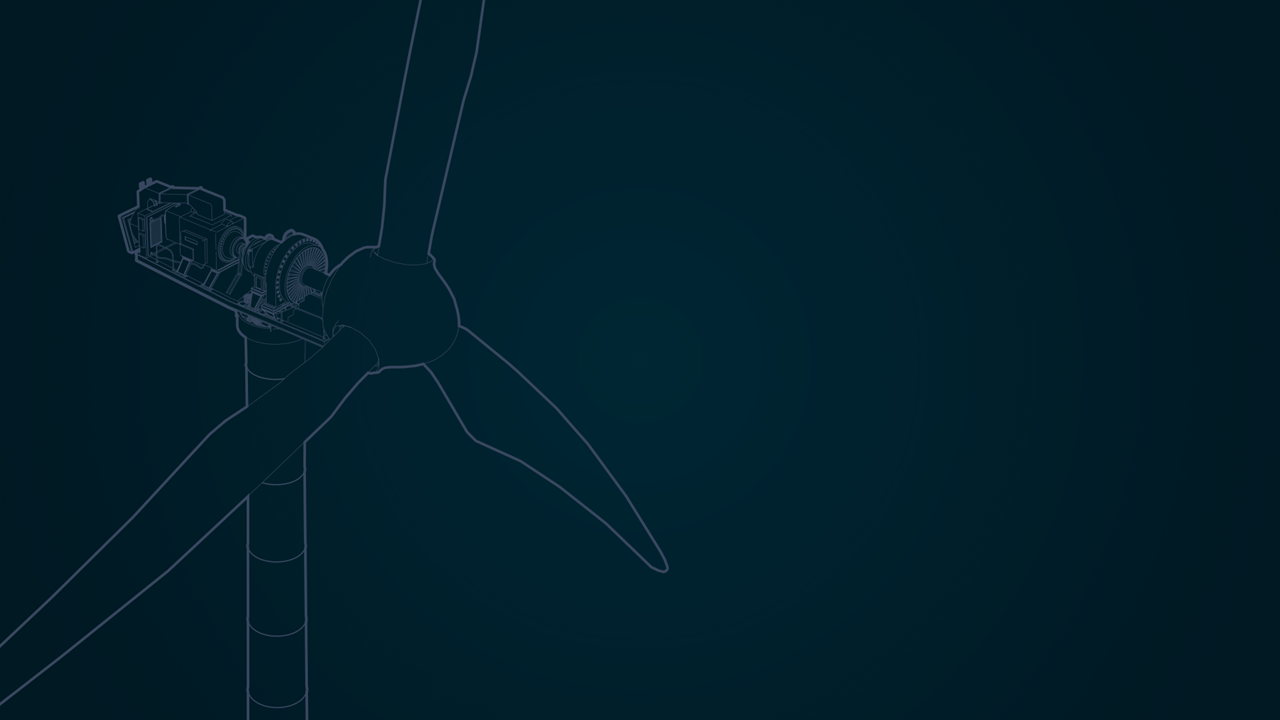
As wind turbines get bigger and situated in harsher environments, remote preload monitoring has the potential to become indispensable for future wind energy.
Read moreAs wind turbines get bigger and situated in harsher environments, remote preload monitoring has the potential to become indispensable for future wind energy.
Read more